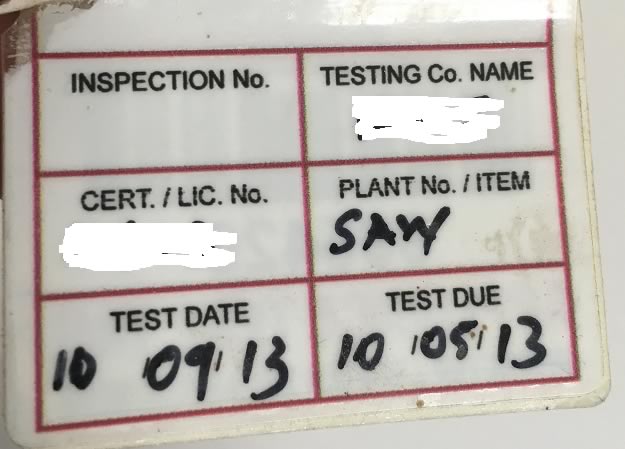
Can Non-compliant Tags Invalidate Your Program
28/09/2017
What Is RCD Testing
24/10/2017Three Phase Appliance Test And Tagging
The range and type of three phase appliances that are used in workplaces is wide and varied and consideration must be given to including them in your test and tagging program.
Three phase appliances are most commonly found in factories, workshops, manufacturing plants and places of assembly where the appliances are subject to heavier duty workloads. Many forklifts, such as those used in warehouses, require a three phase charger.
Due to the higher voltage used – 415 volts instead of the usual 240 volts mains supply – and often higher amps, three phase appliances can present a substantially higher risk of electric shock injuries to workers, especially if the appliance is defective.
Here is a picture of a typical three phase lead, plug and supply outlet. You will notice the design and size of the plug is very different to the normal appliances you plug into a standard power point.
The most common type of three phase appliances found in workplaces are 10 amp, 20 amp or 32 amp rated appliances with either a 4 or 5 pin plug or socket.
Here are examples of a three phase 5 pin socket and plug
A common mistake made when testing and tagging three phase appliances is to perform the 500V DC insulation test (IR test) when checking the integrity of the insulation. Whilst the IR test is usually ok to perform on three phase extension leads, it should not be performed on three phase appliances because more often than not they require 415V AC to be supplied so the switch can be latched in the ON position and/or complete the internal circuits and enable full and thorough testing to be undertaken. To do this, special test equipment and leads are required to be used by the technician.
ACME Test and Tagging technicians are properly trained and experienced in the correct and safe testing and tagging techniques for a wide range of three phase appliances and leads. …more information about our three phase test and tagging service
Want to learn how to correctly test and tag three phase appliances – contact our training team for upcoming three phase training course.
Case Study:
We took on a new client who ran an extensive manufacturing plant that had a lot of three phase machinery.
Prior to commencing the initial round of testing and tagging for them, they provided us with a report listing all of their workshop appliances and the details of the testing and tagging performed by the previous contractor. A quick look at this report revealed incorrect testing methodology had been applied on all the three phase appliances – the IR test had been performed to check the integrity of the insulation.
By late morning we had already identified four three phase appliances that had leakage current reading well in excess of the maximum threshold permitted under AS/NZS 3760 due to a breakdown of the insulation within the appliances. This type of defect creates an increased risk of electric shock to any user of the appliances. This defect would never be detected using the IR test.
This information is general in nature, should be used as a guide only and read in conjunction with the relevant Standard(s), State and/or Federal Legislation, Codes of Practice and Industry Standards specific to your workplace. A proper risk assessment should be under taken before acting on the information provided in this document or any related material. Further information can also be obtained from your local Workplace Authority, Electrical Safety Authority or a suitably qualified persons. This article is copyright protected.